June 10, 2025 The photography exhibition titled “Saline di Volterra, a Presidential Inauguration (1959)” was…
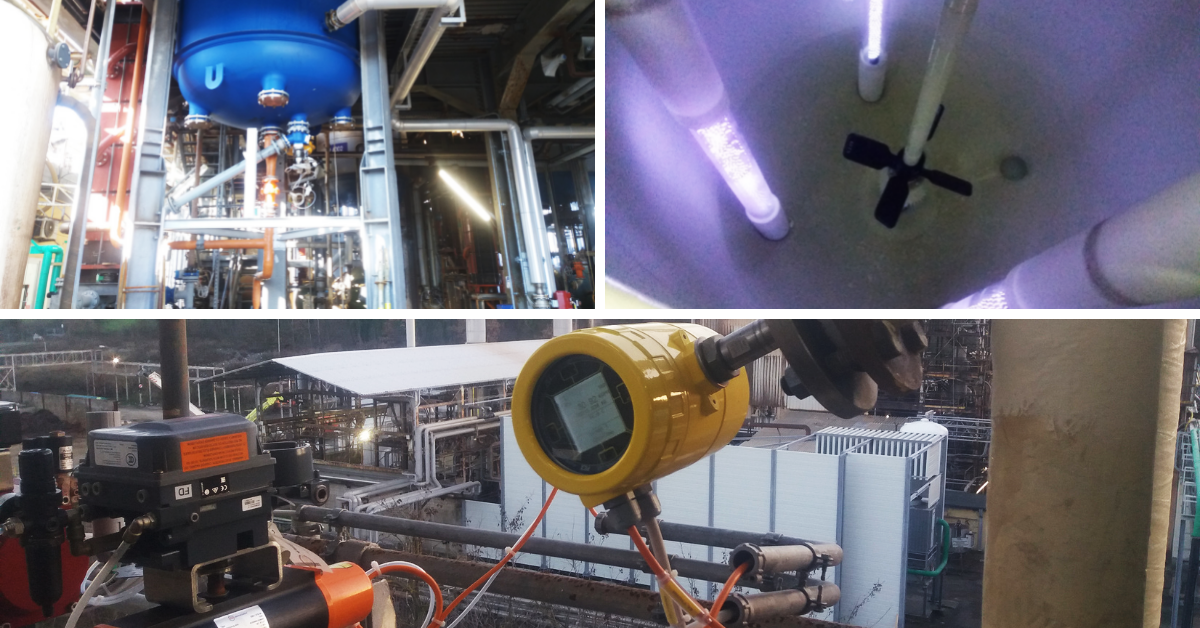
Altair Chimica is adopting a modern and green approach involving the installation and start-up of a fourth reactor for production of chlorinated paraffin in January 2022. The new reactor is completely dedicated to the production of ESSEBIOCHLOR, which is heralded as the company’s new frontier in ‘eco-bio’ chlorinated paraffins, maximising innovation, biodegradability and environmental sustainability.
By installing the fourth reactor, the company will boost production potential at the photo-chlorination plant by 25%, enabling it to meet its production target of 16,000 tons/year.
The chlorinated paraffin plant is the heart of the organic chemistry at the Saline di Volterra plant. The plant was created in 2013 with the installation of the first production reactor, followed by the addition of a second reactor in 2015 and finally a third in 2018. The reaction between chlorine gas and n-paraffin takes place in this system, using light as a catalyst (light energy at a particular wavelength); this type of chemical reaction is also known as “photochlorination”. The plant produces all possible types of finished products, including medium, long and very long-chain chlorinated paraffins as well as environmentally sustainable and highly stable chlorinated paraffins, with the best performance on the international market.
The fourth chlorinated paraffin reactor is the result of many years of research by Altair Chimica’s R&D and Design Department. In fact, it was set through the intersection of Industry 4.0. and the sustainable chemistry industry.
The new installation has many trengths.
1) It’s sustainable, because it operates using a light source without mercury vapour that produces huge energy savings.
This is the first ever reactor to exploit LED technology to catalyse the photochlorination reaction: in addition to substantial energy savings, it marks an important choice in the push towards environmental sustainability. In fact, until now the reaction employed to produce chlorinated paraffins has always been catalysed using mercury vapour lamps, which have a significant environmental impact when they are sent for disposal.
2) It’s 4.0 because it is highly automated and interconnected with the company management system.
Sensors and measuring instruments are installed on the system for the continuous monitoring of operating conditions, control and management of the production process and safety, guaranteeing high levels of automation. All the instruments are connected to the distributed control system (DCS), which is located in the control room, where the signal acquisition boards and CPUs (central processing units) are housed. Each section of the equipment has its own synoptic table, represented on a computerised display, which is used by the control room technician to supervise operations. But the real innovation is how the system interfaces with the company management software, enabling the machine to communicate with the person entering sales orders and receive information about availability and production forecasts for finished products. This sophisticated person-machine connection represents a prototype that Altair Chimica designed independently and is now experimenting with as a pioneer in global technology.
3) It’s smart because it incorporates a cutting-edge flow meter.
The thermal mass flow meter is the latest innovation in research and development on gas flow meters. The company is undertaking an industrial-scale pilot installation, exploiting the principle whereby a fluid removes heat from a heated body as it passes, thereby succeeding in measuring the flow rate of the chlorine gas feeding the production reactor with extreme reliability, thus supporting health, safety and work quality.
Therefore by using increasingly advanced technologies and synthesis strategies that respect the environment and worker safety, Altair Chimica continues to establish itself as an example of a GREEN and SMART company, which works every day to promote useful and sustainable innovation in products, process and technologies.